How to Use a Power Drill
Cordless technology certainly has been a boon to the drill market, but two other advances may have made a bigger change in how a drill is used. The keyless chuck and the easy-reverse feature transformed what used to be little more than a hole-maker into a handy drill/driver. Using the reverse button and keyless chuck together reduces bit changes to about 3-4 seconds, and gone are the days of fumbling for the chuck key.
Of course, a standard 3/8-inch drill is still a very simple, straightforward tool, and you might not think there's much to know in terms of technique, but like a scalpel in the hands of a gifted surgeon, it's the operator's touch that makes all the difference (the right bit never hurts, either). Here's how to use a power drill.
Lickety-Split Bit Changes
You need 3 things to start making the most of a standard ⅜" power drill:
- a set of good twist bits (or brad-points; your choice)
- a magnetic screw tip holder and tips (for driving screws; I prefer the longer, 3-inch holder)
- a combination piloting-countersink bit (for countersinking screws in wood).
Unless you own more than one drill, you'll be swapping among these three pieces a LOT. Here's how to do it quickly: wrap the thumb and forefinger of one hand around the chuck and hold on tight; use the other hand to flip the drill into reverse, then pulse the trigger to spin the motor backwards, opening the jaws of the chuck. Insert the bit and hold it centered with the thumb and forefinger of the first hand, grasping the chuck with your middle and third fingers this time. Flip the drill into forward and pulse the trigger to tighten the chuck onto the bit. Done.
Watch Your Speed
Standard drill bits are designed for wood, metal and plastic (you need specialty bits for things like masonry, glass and ceramic, as tile contractors in Baltimore know). But it's important to adjust your drill speed—and how much pressure you apply—based on the material you're working with.
For rough holes in wood, high speed and pressure are fine, but pushing hard increases the chance of tear out (see below). To minimize splintering when starting a hole in wood, it helps to go a bit slower and to keep the bit as straight as possible.
When drilling metal, use a slow speed and relatively light pressure. Too much of either overheats and dulls the bit very quickly. Sometimes it helps to vary the pressure, pushing harder briefly to help the bit bite into the metal, then easing up and letting the bit do the work. You can also add a drop or two of household oil to the hole as you drill to reduce heat buildup.
Plastics tend to be the same as metal: If you go too fast, the plastic melts; if you press too hard, brittle plastic can crack.
Preventing Tear Out
Drilling through any wood material involves the risk of splintering caused by the bit exiting the wood on the backside of the hole—that's called tear out. There are two basic methods for preventing, or at least minimizing, tear out.
The first works only with hole saws and bits that have guide points, such as spade bits. A carpenters' trick is to drill through the wood from one side, stopping as soon as the guide point (or the center bit on a hole saw) penetrates the backside of the material. Then flip the work over and complete the hole from the backside; the hole made by the guide point centers the bit for the second half of the hole.
The other way to prevent tear out works with all bits. Simply clamp a sacrificial backer board—any flat piece of scrap lumber will do—to the backside of the work piece. Drill all the way through the work from one side, going into the backer board a bit before retracting the bit. The backer board supports the wood fibers on the back face of the work to prevent splintering.
Good Driving Habits
Driving screws properly with a drill takes experience and focus. Expert operators seldom strip screws, while rookies do it all the time. Why? Experts follow three basic rules:
- keep the drill straight
- apply a lot of pressure
- know when to let off the trigger.
The first two rules are self-explanatory; the third comes with experience. But if you follow the first two rules, often the screw (and the material) will let you know it's time to stop driving. If you're still stripping or breaking screws, you're stopping too late and/or you need pilot holes (or bigger pilot holes).
Many cordless drills have a clutch feature that stops the chuck from spinning at a preset torque level to help prevent overdriving or stripping screws. I think that "smart" hands work better than a clutch.
Allowing for restrained wrist movement provides some give to prevent over-torquing the screw, and a quick trigger finger stops the power altogether. Pulsing the trigger after the screw is driven home gives it a final tightening, but this requires extra care, as inertia increases the chance of screw breakage. Above all else, if you focus on what you're doing and consider the forces at play, you'll strip a lot fewer screws.
Buying a New Drill
Every tool hound knows that choosing the "best" tool is a highly personal process. This goes double for drills. Not only should a drill feel just right in your hand, it also must have the response and performance you want. I have a cautionary tale to share after recently replacing a beloved DeWalt corded drill. Sizing up the models at the store, I succumbed to the usual male urges and opted for the most powerful tool on the rack.
This was a mistake. The drill I got is certainly well made, but it's a bit too heavy, too fast and too powerful for the kind of finessing I was used to with my old drill. It feels like a muscle car instead of a nicely engineered sedan. The extra power may come in handy for driving concrete screws or mixing grout, but I don't do those things very often. In retrospect, I wish I could have tested the drills for bit changes, drilling and driving before making the purchase.
Philip Schmidt writes for Networx.com.
Updated December 24, 2018.
Looking for a Pro? Call us(866) 441-6648
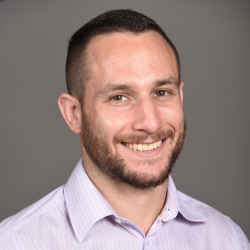
Carpentry Average Costs
Carpenters Experiences
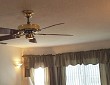
Drywall Repair Drama: And The Leaks Went On And On
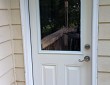
A Professional, Punctual Back Door Replacement
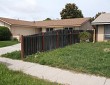